All-Electric: A Path to Home Decarbonization
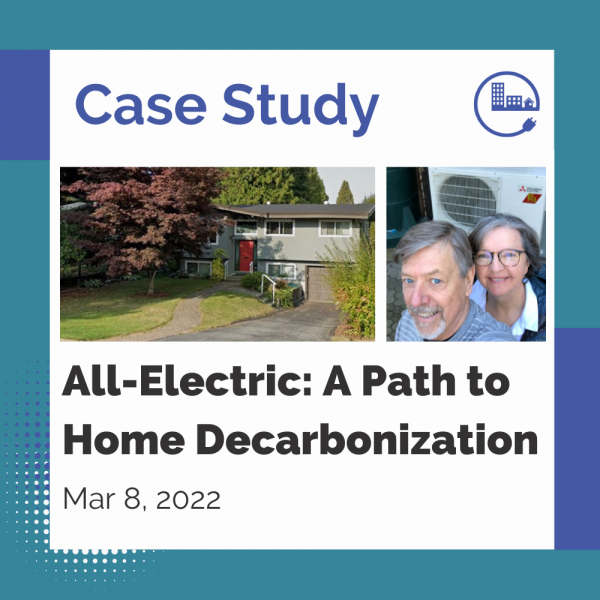
All-Electric: A Path to Home Decarbonization
Gary and Sharon Hamer set a goal to answer an important question: Can we renovate our 55-year old home to Net Zero emissions? Spoiler alert: the answer is Yes!
Starting with the end goal in mind, the Hamers embarked on a mission to reduce their family’s carbon footprint by taking a stepwise approach to full decarbonization. In July 2021, they reached a pivotal milestone: turning off their gas meter and cancelling their gas account!
As an energy professional, Gary Hamer has plenty of connections in the industry. He knows the right questions to ask and how to find the right contractors to do the job. The intention of this series is to share this knowledge, making it easier for other motivated homeowners to follow his lead. Part one of this two-part series tells the story of the homeowner journey; stay tuned for part two which offers advice on how to work with a heat pump contractor to get the best experience
Image 1 (left): The Hamers’ two-level home was built in 1965 and has a heated floor area of 200 m2 (2,200 sq ft). It is located in Climate Zone 4, the most moderate of the six climate zones in British Columbia and an ideal climate for full electrification. Image 2 (right): Einar Halbig performing a blower door test to measure air leakage.
The House
In March 2021, the Hamer’s hired Einar Halbig, owner of E3 Eco Group, to evaluate their home performance in preparation for a deep emissions retrofit. The home was rated at 86 GJ/yr; a typical new home would use approximately 61 GJ/yr. On Gary’s main floor, windows make up 14% of the wall area and account for 15% of the home heat loss. The home’s EnerGuide report estimates thermal resistance of the wall and roof to be RSI 1.7 (R10) for the walls and RSI 3.4 (R19) for the roof. The higher the resistance or “R” value, the slower the rate of heat transfer through the insulating material.
The Process: Getting off Gas
Step 1: Air Sealing and Envelope
The quest to improve the home’s energy efficiency started when the Hamers purchased it in 2001. A blower door test revealed air leakage of 14 air changes per hour under slightly negative pressure (ACH50). In that year, two open-hearth fireplaces were closed off. One was replaced with a sealed-combustion natural gas fireplace; the other, sealed with foam to stop drafts and heat loss up the chimney. In 2002, they replaced the original aluminium-frame single-paned windows (USI = 5.7) with vinyl-frame windows that are double-glazed, argon-filled with low solar gain film, with USI value less than 2 (current code requirements are USI <= 1.4). Over the next decade, the Hamers completed several retrofits and renovations to improve their home comfort and increase the home’s energy efficiency and airtightness. While finishing the basement the Hamers added insulation to the walls and concrete floors. “Those basement bedrooms are now the most comfortable rooms in our home,” says Hamer. The latest blower door test, conducted in 2021, showed that the envelope upgrades had reduced air leakage by more than half to 6.3 ACH50.
Step 2: Efficiency Upgrades & Domestic Water Heating
In 2005, they replaced a 40-year old natural gas furnace with a new furnace that was half the size and 50% more efficient. They also switched their water heater from gas to a premium electric resistance tank and eliminated their old exhaust flue. When the water heater needs replacement in the next decade (or longer), they anticipate installing the highest quality heat pump option available.
Step 3: Cooking
In 2018, a major kitchen and bathroom upgrade was undertaken to make the home more functional. As part of this work, they installed a new gas stove and cooktop with a downdraft fan. The Hamers soon regretted this decision. The downdraft fan did not effectively draw the cooking smoke down and resulted in poor indoor air quality. Gary read about the negative health effects of indoor gas combustion and made the expensive decision to fix the problem by installing a good range hood and replacing the gas cooktop with an induction cooktop. With the help of Gary Milligan from Hugh Milligan & Co and following best practices, they chose a locally-built range hood, Victory Range Hoods, that was wider than the cooking surface and vents cooking byproducts up and through the attic. An electrician installed the required 40 amp circuit and Martin from Handy Appliances installed their Bosch Benchmark induction cooktop.
“We love how quickly and accurately our new induction cooktop responds. We can boil water in less than a minute! It looks great and it is safer to use and way easier to clean than our previous gas cooktop was,” says Sharon Hamer. “The ‘cooking with gas’ campaign from the 1940s was a huge success, but I think that anyone who tries an induction cooktop will never settle for anything less. Induction cooking has the best control and highest efficiency while being safer and healthier for everyone in the family. Once you realise that you don’t need gas in your kitchen, whole-home electrification seems easier to achieve. We do not need natural gas to provide any of the services in our home,” states Gary. And with that in mind, the Hamers set a goal to completely “get off gas”.
Image 3 (left top): Before and Image 4 (right): After. Image 5 (lower left): Typical induction cooktop surface.
Step 4: Lawn Care, BBQ, Transportation
The Hamer’s took their zero carbon goal seriously by swapping their gas mower for a push mower, scrapping their propane BBQ in favour of a wood pellet grill and trading two gas vehicles for one electric SUV. The new vehicle they chose was the Tesla model Y because of its range, minimal maintenance, emissions reduction (2+ tonnes of CO2e per year), hauling capacity, life expectancy and safety. “I promote heat pumps at work, and the model Y was the first Tesla to have one. That made our decision much easier!” Gary jokes. “Charging the car in the garage overnight rather than at a gas station was the icing on the cake.”
Image 6 (left): Gary and Sharon with their new electric vehicle. Image 7 (centre) Push mower. Image 8 (right) Wood pellets for BBQ cooking.
Step 5: Space Heating
Switching out the gas furnace for a heat pump was the most challenging step in the Hamers’ decarbonization journey. The number of decision points in this process seemed daunting, but with some help, they found the right solution for their home. Rob Pope, Ecolighten, provided the heat loss analysis to size the system and Dave Hoare, Midtown Heating and Cooling, provided a recommendation on the heat pump model. After measuring the supply ducts and the static pressure when the furnace was operating, Dave recommended the Mitsubishi Zuba with Hyperheat for all-weather performance and indoor comfort. In addition to making some of the most efficient heat pumps available, Mitsubishi requires specific training for installation contractors, and they have strong local technical and training support. The Zuba is designed for cold climates (perfect for Canada!); this means that during the winter, the Hamers stay comfortable without the need for a back-up heating system. The heat pump also provides cooling for increasingly hot summers. By selecting the most efficient heat pump model and ensuring it is right-sized, indoor comfort is maximized year round and the Hamers use less energy to operate the system.
Image 9 (left): Dave Hoare, Midtown Heating and Cooling posing in front of the newly installed heat pump. Image 10 (right): Heat pump exterior unit in 2021 cold snap.
Results: How it’s going
The Hamers reached their goal of “turning off the gas” on their wedding anniversary in July. With the induction cooktop in the kitchen and winter months away they knew that they had plenty of time before space heat was needed. Installed in September 2021, the heat pump was put to the test and worked well during the long cold snaps in December and January when the temperature dropped to -21oC. It operated quietly while providing consistent indoor temperatures all winter long. Through the HydroHome app, Hamer monitored how hard the heat pump was working with varying outdoor temperatures. Inside, occupants were kept comfortable with the heat pump quietly maintaining a very consistent indoor temperature. They are also looking forward to the cooling benefits the heat pump provides as the summers get increasingly warmer.
The Hamer’s overall cost to convert their heating system to electric included both an electrical service upgrade and a heat pump installation. The heat pump system installed was $17,000. Because the Hamers opted to plan for onsite electrical generation (solar PV) and storage (batteries) in the future, at $12,000 the new electrical system is more expensive yet more versatile than a basic upgrade would have been. Not every home will need an electrical system or panel upgrade for a heat pump installation, but it is an important consideration that should not be overlooked.
Local, provincial and federal incentives can help to reduce the capital cost. Theoretically eligible for $12,000 in provincial and municipal heat pump & upgrade incentives, they missed the federal incentive due to the complexity of the program details and settled for $7,000 in provincial incentives.
The Hamers' motivation to disconnect their natural gas line was largely due to their desire to mitigate their contribution to climate change while improving the comfort and resiliency of their home. While they celebrate the fact that they are no longer paying for a gas service which included $150/yr in fixed fees, the cost of gas, and $135 in annual carbon taxes (which is projected to rise annually), they may not end up saving on their overall energy bills. Hamer says, “I know our heat pump will be at least twice as efficient as our old furnace; however, to save money on its operation we need it to be three times more efficient. Using data from October to January, it appears our heat pump was 2.4 times more efficient than the furnace. To me this shows that, properly designed and installed, heat pumps can be a very cost effective heating solution.”
“We are most excited about the non-energy benefits of heat pumps. Year-round comfort and health! We didn’t do this to save money on our energy bills but rather to provide us with a better home.” The heat pump has reduced the Hamer’s carbon emissions by 3 tonnes per year, which is equivalent to the carbon sequestered by 1.5 hectares of temperate forest each year.
Future Planning
Planning a decarbonization journey in advance of equipment failure is ideal to ensure the best outcomes. When furnaces fail in the middle of winter, homeowners do not have the luxury of time to plan for a replacement. Factors like installation timelines can be managed with good planning. In the Hamers’ case, the heat pump project took longer than anticipated due to delays in permits and inspections, scheduling trades, equipment delivery, and pouring concrete pads.
Future-proofing and resiliency were key decision factors in choosing the way the electrical service was designed and installed just before their heat pump upgrade. They planned for the future integration of onsite energy storage, generation and power management. With minimal changes to the electrical system they can now include these elements when it makes sense for them.
Starting with a desire to mitigate their impact on climate change, the Hamers decarbonization journey uncovered opportunities to accomplish their goal and provide them with a more resilient and comfortable home. As Gary says, “It just takes a little planning!”
Stay tuned for part 2 of this article: Tips for homeowners looking to purchase a heat pump.