Decarbonization Through HVAC Retrofits
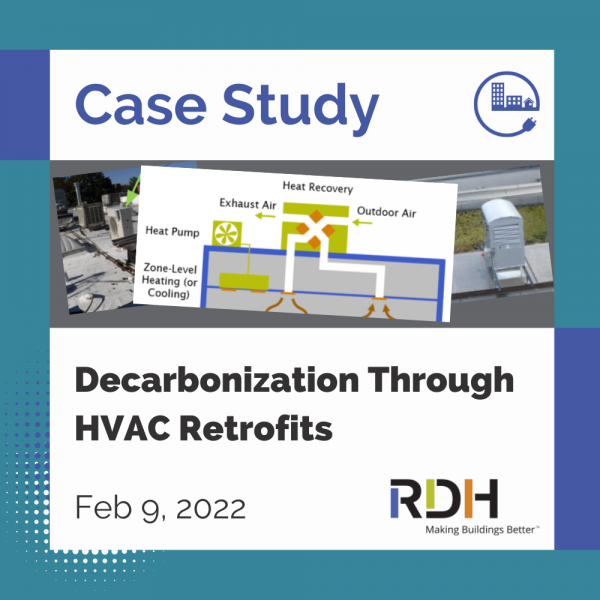
Decarbonization Through HVAC Retrofits - Solutions for Small Commercial Buildings
Background
The small commercial building sector comprises a significant proportion of the commercial building floor space in BC. Think strip mall retail units, smaller office buildings, smaller schools, clinics etc. Common characteristics of many of these buildings are that they have similar Heating, Ventilating and Air-Conditioning (HVAC) systems and have historically been underserved by incentive programs and other supports to help them save energy and reduce emissions. This is changing.
RDH Building Science managed an 8-building pilot program for the Northwest Energy Efficiency Alliance between 2014 and 2019 that demonstrated a low-carbon HVAC upgrade solution uniquely suited to small occupied commercial buildings. Through the pilot we achieved dramatic reductions in total energy consumption (up to 61%) and greenhouse gas emissions (up to 90%) while in many cases significantly improving occupant comfort. We also completed all of the projects with no or minimal business interruption.
Lessons learned were thoroughly documented and a performance specification developed from those lessons learned to guide other similar buildings to successful outcomes. Even better, CleanBC now offers incentives (via the Custom Lite program) to support this type of upgrade for smaller commercial customers in BC.
The Concept
HVAC typically accounts for 30% to 50% of the energy end use in commercial buildings. Small commercial buildings will often utilize a packaged rooftop unit (RTU) system that includes direct expansion (DX) cooling and natural gas heating to provide space conditioning and ventilation air from a single source.
This approach leads to system inefficiency and potential air quality impacts due to several factors, including:
- The inability to separately control ventilation based on occupancy while controlling space conditioning based on temperature setpoints, which leads to excessive energy use.
- The equipment tends to be oversized, and as it reaches the end of its service life, contractors simply replace like for like. Engineers are not typically engaged to confirm or refine the sizing and specification of systems in these small commercial buildings.
- Anecdotal evidence indicates that outdoor ventilation air dampers in existing packaged systems are often left closed in these buildings, leading to poor indoor air quality.
An alternative design approach is referred to as a Dedicated Outdoor Air System (DOAS), which decouples the ventilation and space conditioning functions. As verified in our pilot, if ventilation air is provided with an intelligent, very high efficiency heat or energy recovery ventilator (HRV/ERV), and if the heating and cooling functions are provided by right-sized, high-efficiency systems, annual total energy savings can exceed 50% over the existing system. The use of such a system also allows for a reduction in peak demand and improvements to indoor comfort compared to the standard RTU design.
The Buildings
The table below lists the buildings that were upgraded through the pilot. Included were four offices, one office/service garage, two restaurants, and one dormitory. Six were located in milder coastal climates in Washington and Oregon, and two were in cold climates in Montana.
|
|
|
|
|
|
|
|
|
|
|
|
|
|
|
|
|
|
|
|
|
|
|
|
|
|
|
|
|
|
|
|
|
|
|
|
|
|
|
|
|
|
|
|
|
|
|
|
|
|
|
|
|
|
All buildings were retrofitted with a very high-efficiency HRV system to provide the required building ventilation while minimizing the heating and cooling load for conditioning ventilation air, typically making use of the pre-existing ductwork. The HRV used in all pilots was the Ventacity VS1000 outdoor unit (this product plus a larger option are now available in Canada). It has a sensible heat recovery efficiency of 83 to 91% in cooling and 85 to 93% in heating, and a fan efficacy of 3 to 6 cfm/Watt.
A heat pump system was then designed and specified to meet the remaining heating and cooling loads. In some instances, this resulted in a “right-sizing” of the equipment, which increased energy and peak demand savings. Air-to-air heat pumps were used for all the buildings, although the system configuration varied by project (ductless mini-split, ducted central systems of various types). Air-to-water or other heat pumps delivering heating/cooling hydronically would also be an excellent solution for this conversion approach, although none were secured for this pilot.
Results
Physical Impacts
Below are images that visually demonstrate the downsizing potential of this type of system conversion. Building #7 is an office building with very large RTUs that were over-ventilating and doing a lot of zone level reheating.
Removal of the old RTU from Building 7. The equipment to the left of the RTU is the new VRF heat pump outdoor unit that was installed prior to removing the RTU.
Building #7’s RTUs were replaced with HRVs for ventilation. The HRV shown here is installed on the old RTU’s pad and uses the existing ductwork to distribute ventilation air. The outdoor unit for the new VRF heat pump system (for heating and cooling) is on the left side of this image. The building was able to replace 95 tons (334 kw) of cooling with 32 tons (113 kW). The heating capacity was maintained. This conversion saved close to 70% total energy.
Energy and Emission Savings
The total and HVAC energy savings achieved for the 8 pilot buildings are summarized below. Factors that influenced the magnitude of savings included the proportion of energy consumption dedicated to the HVAC system versus the remaining building load that was not impacted by the pilot. The ‘typical’ office buildings saved between 42 and 68% of total energy. The two restaurants saved a significant portion of their HVAC energy but saw lower overall savings because so much of their energy is used for cooking. The office/garage in Libby, MT saw slightly lower savings because the garage space had large loading bays that were frequently open for servicing vehicles.
|
|
|
|
|
|
|
|
|
|
|
|
|
|
|
|
|
|
|
|
|
|
|
|
|
|
|
|
|
|
|
|
|
|
|
|
|
|
|
|
|
|
|
|
|
|
|
|
|
|
|
|
|
|
*Only a portion of the building was retrofitted during the pilot period. The verified savings were extrapolated to the whole building.
Below are the energy savings results presented graphically for all buildings except the restaurants (which skew the scale of the y-axis given their high process load consumption).
Given that a primary focus of provincial policy is reducing greenhouse gas emissions, we translated the verified results achieved in this pilot to reflect the emission intensity of BC’s energy grid and estimate the potential emission savings from completing similar projects in BC.
|
|
|
|
|
|
|
|
|
|
|
|
|
|
|
|
|
|
|
|
|
|
|
|
|
|
|
|
|
|
|
|
|
|
|
|
|
|
|
|
|
|
|
|
|
|
|
|
|
|
*Only a portion of the building was retrofitted during the pilot period. The verified savings were extrapolated to the whole building.
The conversion concept enabled full electrification of HVAC systems. Given the disparity in greenhouse gas emission intensity of natural gas versus electricity in BC, projects that currently use natural gas for heating will save more emissions than those that use electricity for heating. This is shown in the graph below, which only includes the office projects that used natural gas for heating prior to the conversion. These three buildings achieved 74 – 90% emissions reductions.
Impact on Peak Demand
Peak demand is the highest rate at which electricity is used during a period of time and is typically measured in kilowatts (kW). BC Hydro uses the annual peak demand, along with total electricity consumption, to determine business General Service Rates. The Small General Service Rate applies to businesses whose annual peak demand is less than 35 kW. Any business that falls under the Medium or Large General Service Rates pay a demand charge in addition to a consumption-based charge. There is, therefore, an added financial benefit for businesses to reduce their peak demand in addition to their total consumption.
The pilot demonstrated the peak demand reduction potential of this conversion concept. The graph below illustrates the peak electricity demand reduction for Building 6, which used electricity for heating prior to the conversion. As shown, peak demand savings are achieved in both winter and summer.
Building 6 peak electricity demand before (left graph) and after (right graph) conversion.
The graph shown below is the peak electricity demand for Building 1, which was heated by natural gas before the conversion. After the conversion, heating is now provided by a heat pump, powered by electricity. As shown, the peak winter electricity demand increases after the conversion, but is still less than the peak cooling demand of the old system, meaning that the annual peak demand is still reduced. This business owner saved on their total electricity bills while eliminating their natural gas bill.
Building 1 peak electricity demand before (left graph) and after (right graph) conversion. Note that natural gas is providing heating in the ‘before’ case and as such is not represented on the electricity demand graphs.
Lessons Learned
The project team interacted with contractors, owners, and occupants throughout the project to identify any challenges with integration and assist in troubleshooting the system where required. This led to the identification of key lessons learned from the project that will assist with future installations as well as broader scale adoption of this retrofit approach. These lessons all informed the development of a detailed performance specification that can be applied to any future project.
- Right-sizing replacement equipment: Our expectation was that the area served per ton of cooling could be increased from a typical 350-400 ft2 per ton (~9-10.5 m2 per kW) to 600-700 ft2 per ton (~16-18.5 m2 per kW) as a result of decoupling air conditioning from ventilation, provided that the new equipment was right-sized. Of the completed projects, some went through a right-sizing exercise and some did not. Building #1, which was right-sized, is functioning well at 725 ft2 per ton (19 m2 per kW). Building #6, which was not right-sized but had a very similar use, building enclosure assembly, and a milder climate compared to Building #1, installed a system with 420 ft2 per ton (11 m2 per kW).
- In several of the pilot projects, the initial contractor bids were based on the same capacities as the old equipment. They also tended to rely heavily on design assistance from heat pump equipment suppliers, typically leading to more zones and extra features that added cost for what was intended to be a simple system. If an owner acquires a bid that seems financially infeasible, it is worth a second look. There may be too many zones or unnecessary control features in the bid. While final costing data was not provided for all projects, $15-16/ft2 ($160-170/m2) total installed costs were reported for several of the projects.
- Specification and procurement: The pilot relied on a single HRV model as it was the only unit available with sufficiently high heat recovery efficiency, controllability, and very low fan power. A less efficient HRV may mean that supplemental heating of ventilation air would be required, which would both reduce energy savings and increase the project cost to add a pre- or post-heater. If a less efficient HRV is used without supplemental heating, occupants may find the incoming air too cold in winter. At the time of the pilot only one equipment manufacturer could meet the performance specification. This proved to be a challenge for institutional owners with procurement policies that required three bids, and the pilot had to rely on the project owners to resolve this issue in their own way.
- Air leakage and commissioning: As mentioned previously, many of the buildings repurposed the existing ductwork for the new ventilation system. During the commissioning process airflow rates were measured at the HRV supply diffuser outlets. In most installations, the supply airflow at the outlets was found to be lower than the design conditions by up to 25%. The initial solution from contractors was to increase the airflow rate at the HRV by adjusting the flow setting until supply flow rates were met. Although this could correct for the undersupply of ventilation air, it increased the energy consumption of the system (for two reasons: the HRV has to work harder to supply more air and it’s less efficient when running full capacity than when running at part-load). Further investigation into the root cause identified a number of locations where air leakage could be felt from the ductwork at fittings. Efforts to improve duct seals reduced the amount of unwanted leakage. The work identified challenges with repurposing existing ductwork due to the potential leakage and the importance of preventing duct leaks in the lower-airflow DOAS designs compared to standard recirculating air systems. Leakage of unconditioned air into HRV ducting can seriously compromise the performance of this part of the system, and proper commissioning is very important.
- Occupant education: Another key to achieving significant energy reductions was the proper setup and operation of the new system. Building owners/operators were required to change how they operate the HVAC system to account for the separation of the ventilation from the air conditioning systems, which increased the number of control panels within the building. Initial feedback from some building occupants identified hesitation to adjust the setpoint temperature despite dissatisfaction with the indoor temperature. Others made changes without understanding the impact or expressed confusion about which controls to adjust to solve a particular comfort issue. Proper instruction around the intended system operation, as well as periodic follow-up (for example, part-way through each season for the first year) is required to ensure both comfort and energy goals are achieved.
This was an exciting project that exceeded the team’s expectations in terms of the verified energy savings achieved, while also improving the occupants’ perception of comfort and air quality. In a time when extensive retrofit work is required across all sectors to meet urgent carbon reduction targets, building owners and operators can draw on the extensive supportive resources developed through this pilot and the incentives now available to implement a viable solution for their small commercial buildings.
To Learn More
- The performance specification can be found here:
- An installation guide has also been developed by NEEA and can be downloaded here:
- CleanBC is offering incentives to support this type of upgrade through its Custom-Lite incentive program.
Author: Christy Love, P.Eng., Principal, RDH Building Science