Fraser Pointe 1 Hybrid Domestic Hot Water Retrofit
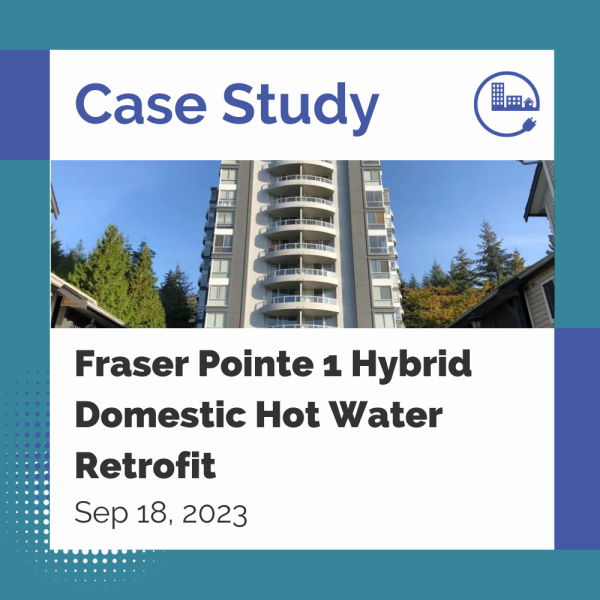
98% of BC’s electricity is produced through hydroelectric generation, offering a plentiful, low-carbon energy source. However, 66% of residences in BC heat their water with gas, and domestic hot water (DHW) heating is responsible for 39% of the province’s residential GHG emissions. While new technologies and incentive programs are making it more feasible and attractive for households to convert to climate-friendly electric resistance and electric heat pump hot water systems, decarbonizing domestic hot water systems in existing multi-unit residential buildings (MURBs) remains a daunting proposition.
Built in 1991, Fraser Pointe I is a 16-story market-rental MURB in East Vancouver owned by Concert Properties. Based in Vancouver, Concert Properties owns and manages over 14 million sq. ft of commercial real estate, including 2 million sq. ft of multi-family residential real estate, and has a strong commitment to making their properties as efficient and sustainable as possible. The building’s original DHW system was comprised of two standard-efficiency gas-fired boilers and three 120-gallon storage tanks located on the roof of the building. In 2020, as the system was approaching the end of its service life, Concert Properties retained SES Consulting to undertake a BC Hydro-funded energy study to explore options for a low-carbon replacement. A follow-up study supported by the CleanBC Custom Program was carried out in 2021 to analyze system electrification options in greater depth.
Design Concepts
Schematic of the original system (2019)
As part of the CleanBC study, SES Consulting developed three design concepts for the replacement of the gas-fired DHW system at Fraser Pointe I, along with a base case of replacing the existing boilers with new condensing units.
-
Full electrification of the system with electric-resistance boilers.
-
Full electrification of the system with air-source heat pumps.
-
A hybrid system which relied primarily on ten air-source heat pumps and five 120-gallon storage tanks, along with two high-efficiency gas boilers to handle peak demand and provide full redundancy.
Designing a Cost-Effective Solution
Concert Properties elected to pursue the hybrid option for several reasons:
-
The building’s roof did not have the structural capacity to handle the full electrification with air-source heat pumps option without major and costly upgrades.
-
It offered a significant degree of operational redundancy, with both the heat pumps and high-efficiency gas boilers able to function independently if required.
-
It offered the most cost-effective opportunity to substantially reduce emissions, with the lowest cost in terms of net present value (NPV) per tonne of CO2e reduced over the expected lifetime of the system.
In summary, the hybrid option offered the potential to significantly decrease emissions while reducing implementation and operational costs and avoiding major technical barriers. The system was projected to reduce DHW-related emissions by 75%, or 96 tonnes of CO2e/year.
Comparison of the environmental performance of the three design concepts for the replacement of Fraser Pointe 1’s gas-fired DHW system with a like-for-similar baseline scenario.
The hybrid nature of the new system made for a complex design exercise, with considerable precision needed to accommodate the spatial constraints of fitting all of the equipment on the building’s roof. Structural and acoustic engineers were engaged to ensure that the roof could handle the increased weight of the new system and that the roof-mounted air-source heat pumps wouldn’t disturb residents or neighbours. An electrical load assessment confirmed that the building had sufficient spare capacity to support the air-source heat pumps, though a new electrical feed to the rooftop mechanical room would be required. The presence of new rooftop equipment required a combined building and development permit to be obtained from the City of Vancouver.
Schematic of the new system
As the mechanical design was being developed, a water meter was installed on the existing system to provide hot water use data to right-size the new system. The resulting data revealed actual consumption to be lower, and with a different usage pattern, than predicted by standard industry design tools. This, along with the use of additional storage, allowed for the overall heating capacity of the new system to be significantly reduced compared to the original system: from 1,200 MBH to approximately 650 MBH (400 MBH gas boilers, 150 MBH heat pumps, and 100 MBH electric heater). The difference between predicted and actual consumption was likely due to a combination of factors, including overly conservative industry assumptions about DHW use; installation of lower flow appliances by Concert Properties in the years since the original system was built; and changes in residents’ water use patterns as a result of the COVID 19 pandemic, with lower levels of peak demand in the mornings and evenings and more even distribution of hot water use throughout the day. This finding underscores the importance of using real consumption data for equipment sizing wherever possible instead of relying on handbook or modelled values.
The Best Laid Schemes
Primary construction of the new hybrid system took place in 2022. In an effort to realize certain efficiencies, Concert Properties elected to have the building’s roof replaced at the same time. The two project teams put systems in place to facilitate communication and coordination, and took precautions, such as the installation of temporary boilers to ensure the continuous supply of hot water, to reduce the impact of the project on tenants.
Despite best efforts, the overlap created tensions and confusion between the two projects, and several complications were encountered during construction. The lesson learned was to avoid having multiple concurrent projects with overlapping scopes where possible, as the anticipated benefits and efficiencies are unlikely to outweigh potential conflicts and issues that arise.
Another obstacle emerged when the time came to run the additional electrical cables to the rooftop mechanical room. This was necessary in order to power the SANCO2 air-source heat pumps – which are themselves noteworthy because they use carbon dioxide (CO2) gas as the refrigerant instead of more typical chemicals, such as R410A, that have much higher global warming potential. The original design and contractor proposals called for the cables to be run through stacked electrical closets in the interior of the building. However, during construction, it was discovered that there wasn’t enough space in the electrical closets to accommodate the machine needed to core the new riser. An alternative solution – running the cables to the roof through the building stairwell inside of a fireproof shaft – was quickly identified (though as illustrated below, this resolution created its own challenges). In retrospect, the issue with the original design could have been identified earlier by employing an Integrated Design Process, involving a contractor or specialist with knowledge of the specific equipment used for the coring procedure in the design-phase of the project.
The new means of running the electrical cables required a revised building permit, which delayed the project by several months. As this occurred mid-construction, after the original boilers had already been removed, it created a further complication, as the temporary boilers were not designed to be used for an extended period.
To resolve this problem, the decision was made to start up the new DHW system prematurely with only the gas boilers in operation, as the heat pumps could not be used until the new electrical cables had been run and the necessary power was available. This flexibility proved to be an unexpected benefit of the hybrid design, as the team had actual hot water consumption data for the building and was confident that the system load in the building could be serviced by the new boilers alone. The successful interim operation of the DHW system – using gas boilers significantly downsized from a total of 1,200 MBH to 400 MBH – confirmed the extent to which the original system had been oversized compared to the current need of the building.
The Importance of Performance Commissioning
The new DHW system was commissioned upon installation. However, when its performance was evaluated, it was found to have a number of faults that significantly compromised its GHG savings potential. These took several months to identify and resolve.
For example, once the heat pumps were finally powered up, performance reviews of the system revealed that the majority of the building’s hot water heating load continued to be served by the boilers, with the heat pumps operating only intermittently. Ultimately, the excessive boiler operation was found to have been caused by a leftover piece of temporary programming code that had been put in place on the Building Automation System (BAS) during the interim, boiler-only operational phase, and had not been removed when the new program was written. When the temporary code was removed from the BAS, the heat pumps began carrying a greater proportion of the building’s hot water heating load, and system gas use decreased significantly.
Over the next few months, further commissioning issues, related to balancing of flow through the boiler and boiler heating setpoints, were uncovered and resolved. Throughout the commissioning process, the project team made extensive use of metering and sensors connected to the BAS to identify and resolve issues. The experience served as a reminder that even small errors can cause significant operational issues in complicated systems, and points to the importance of in-depth performance commissioning on new systems, using data to verify performance and troubleshoot issues that arise.
Operational Best Practices
The process of transitioning the new system into ongoing operations highlighted the need to ensure robust training of and support for the building operations team. The traditional “handover” documents and process proved insufficient to bring staff up to speed on a new, complex system that featured not only unfamiliar components but also an additional objective beyond generating hot water: reducing GHG emissions and energy use.
To address this gap on future projects, SES recommends developing an operations guide for building staff to:
-
Provide a straightforward overview of system operations,
-
Explain the purpose of different components,
-
Help building operators interpret what they will see on the BAS, and
-
Provide tips for adjusting and troubleshooting the system without compromising performance.
Performance
Graph illustrating whole building natural gas use, comparing “baseline” (average consumption from 2019 – 2021) and August 2022 to May 2023, along with target and actual cumulative savings.
The new system was put into operation in August 2022. In the first few months, modest savings were realized based solely on the increased efficiency of the new boilers. Gas use dropped further in October, when the sequence of operations was corrected, and the heat pumps became fully operational. Performance commissioning continued through April 2023 and the system was dialed in by May. Even as troubleshooting and commissioning was ongoing, however, the system was quite close to meeting its target savings, as illustrated in the green and purple lines in the graph above.
A B2E Publication written by SES Consulting
Primary Authors: Omar Bhimji and Brad White