Importance of Pre-Changeout Procedures to Optimize Heat Pump Performance
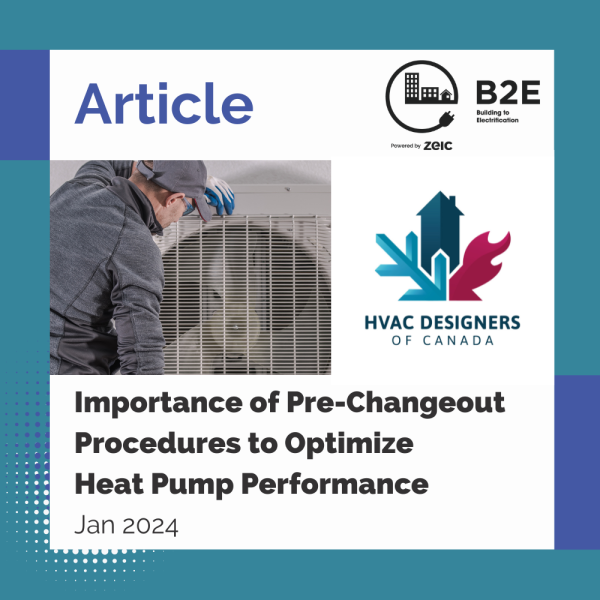
The installation of a new centrally ducted heat pump in an existing home provides an excellent opportunity for homeowners to improve home comfort, save energy, and reduce their carbon footprint. However, to achieve optimized performance, a comprehensive approach by contractors that considers proper sizing, quality installation, and commissioning is required.
This approach starts with pre-changeout procedures that are designed to better understand the existing HVAC system and overall home performance that should inform proper heat pump sizing and equipment selection.
As part of pre-changeout, the following steps should be considered by HVAC contractors and homeowners to achieve optimized performance of a centrally ducted heat pump:
Step 1 – Homeowner Discovery
Homeowner discovery is a process of gathering information from the consumer to better understand their expectations and needs. This step is often overlooked to support informed decision-making and recommendations on a new centrally ducted heat pump. When asked the right questions, homeowners have useful feedback on their experience with the existing HVAC systems performance, and motivations for investing in an upgrade. Topics that should be considered by HVAC contractors when gathering input from homeowners include:
-
Have you completed or are you planning other energy upgrades? This is important to understand overall building performance that could influence heat pump sizing and selection.
-
What is your experience with the existing HVAC equipment and distribution system? This type of question allows for exploration of whether the homeowner has experienced hot or cold rooms, noisy ductwork, or equipment short cycling.
-
What are your motivations for upgrading to a heat pump? A consumer might be interested in upgrading to a heat pump due to environmental considerations, interest in home cooling options, accessing rebates, or otherwise. This information helps shape a contractor approach to presenting their proposal for equipment retrofit.
-
Do you have any concerns with the heat pump outdoor unit placement? Finding a suitable location that does not compromise outdoor living space and meets municipal requirements (e.g. setbacks and noise considerations) can be challenging. As such, the opportunity to collect feedback on potential locations from the homeowner should help inform contractor installation options.
Step 2 – HVAC Performance Assessment
A performance assessment of the existing HVAC equipment is critical for gathering empirical data used to inform heat pump options and potential limitations. Since a heat pump may operate at a different cubic foot per minute (CFM) of airflow than the equipment being replaced, it is important to understand the existing ductwork capacity and its ability to accommodate a heat pump. Additionally, the HVAC performance assessment also allows a contractor an opportunity to propose improvements to the distribution system through accessible ductwork modifications (e.g. improved transitions, duct sealing, etc.) or enhancements (e.g. adding return air).
As part of an HVAC performance assessment, contractors at a minimum should complete external static pressure testing, and calculations to determine whether the existing ductwork and fittings are adequate for system distribution and to gather insight into whether the new heat pump will have enough airflow to operate effectively. More recently, the utilization of airflow testing technologies such as the True Flow Grid allows HVAC contractors to gather even more precise CFM readings by using a device that provides an accurate measurement of airflow through a residential air handler. Without question, the combination of static pressure testing, ductwork measurements, and airflow testing is the most comprehensive approach to better understand existing ductwork capacity that should be used to inform heat pump sizing and selection.
Step 3 – Energy Evaluation and Building Performance
Building on the existing HVAC system assessment, the importance of understanding overall building performance through an EnerGuide for Existing Homes evaluation should be a priority for homeowners and contractors. An EnerGuide evaluation by an Energy Advisor provides a homeowner with a comprehensive whole-house view of their building envelope, air tightness, and HVAC system performance. In particular, the building envelope and air tightness details provide guidance on whether non-HVAC solutions should be considered as part of an upgrade project or even prioritized ahead of a heat pump in order to reduce equipment size and better integrate the heat pump with existing ductwork capacity.
For homeowners, completing an EnerGuide evaluation also provides an opportunity to maximize the amount of government and utility rebates available for upgrading to a heat pump. For contractors, an EnerGuide evaluation with building envelope details and air tightness information can be used to inform a Canadian Standards Association (CSA) F280-12 compliant load calculation to properly size the new heat pump for the heat loss/heat gain requirements of the home.
Not to be left out, an initial review of the electrical panel and service as part of the building performance review should be considered since an electrical strategy (e.g. panel and/or service upgrade) to accommodate additional electrical load with a heat pump retrofit may be needed as part of the project.
Step 4 – Load Calculation and Balance Point
A CSA F280-12 compliant load calculation should always be completed to help right-size the heat pump for the home. Any rule-of-thumb approach to equipment sizing without an actual load calculation should be avoided since older space heating equipment as a reference may not have been sized correctly and existing home conditions may have changed. Of note, both a CSA F280-12 compliant block load that considers the heating and cooling needs for the entire home or a room-by-room approach that provides a load calculation for individual rooms is acceptable practice provided the tools used for the calculation are compliant with CSA F280-12.
Complementing a load calculation, contractors should also complete a capacity balance point calculation to confirm where the capacity of their proposed heat pump equipment equals the heating requirements of the home. The capacity balance point is calculated by plotting the heat loss of the home against the performance curve of the heat pump to ensure the equipment meets the necessary heat load at the outdoor design temperature where the home is located. For a contractor, the capacity balance point and understanding the outdoor temperature at which the heat pump no longer has the capacity to provide adequate heating for the home is critical to equipment sizing, selection, and determining if supplementary heating is needed and how it should be sized.
Balance Point Visual: Natural Resources Canada “Air Source Heat Pump Sizing and Selection Guide”
Step 5 – Supplementary Heating
For a centrally ducted heat pump, supplementary heating is the additional heat that is needed if the heat pump is not able to keep up with the heating needs of the home during peak cold conditions. This terminology should not be confused with “backup” or “emergency” heat which is a heating source that should only come on if there is a failure of the primary heating system.
With the introduction of cold climate heat pumps, contractors and homeowners have access to new heat pump technologies designed to operate with improved equipment capacity and higher efficiencies at lower temperatures versus traditional heat pumps. As such, utilizing a cold climate heat pump as part of an upgrade solution has the potential to minimize or in some cases eliminate the need for supplementary heating. However, it is important to note that the need and source of supplementary heating should be evaluated on a case-by-case basis.
For all-electric heat pumps, supplementary heating is provided by electric resistance heaters. As part of pre-changeout planning, it is important to size any electric resistance heating to match the requirements of the home since oversizing supplementary heating may lead to additional costs for the homeowner including potential upgrades to the electric panel and/or service that may not be needed. Alternatively, centrally ducted heat pumps can also be paired with a gas furnace that is able to provide supplementary heating as part of a dual-fuel or hybrid system.
Aside from supplementary heating that is integrated with a centrally ducted heat pump, HVAC contractors should also consider any other heating sources (e.g. fireplaces, baseboards, etc.) that may be on-site and contribute to space heating as part of heat pump sizing and selection.
Conclusion
In summary, the importance of pre-changeout procedures should not be underestimated. To achieve optimized performance with centrally ducted heat pump, it is critical to take a sophisticated approach and gather the necessary information that will inform equipment sizing and selection. The approaches to pre-changeout outlined in this article also help mitigate the potential for unintended costs and homeowner disappointment with the poor installed performance of their centrally ducted heat pump.
Building on this article, there are several industry resources available that provide additional knowledge sharing for HVAC contractors and homeowners to reinforce the best practices in heat pump sizing, installation, and commissioning to ensure optimized performance:
- Home Performance Stakeholder Council: “Heat Pump Best Practices Installation Guide for Existing Homes”
- Natural Resources Canada: “Air Source Heat Pump Sizing and Selection Guide”
- Natural Resources Canada – Local Energy Efficiency Partnerships: “Best Practices in Heat Pump Retrofits”
- Canadian Standards Association – SPE17-23: “HVAC Guide for Part 9 Homes”
A B2E publication written by Ryan Coleman, Rob Pope and Dara Bowser on behalf of The HVAC Designers of Canada (HVAC DC).
About HVAC DC
HVAC DC is a national association representing Heating, Ventilation and Air Conditioning (HVAC) designers across Canada. HVAC DC works together with other building sector groups to stay abreast of industry changes and supports its members in delivering quality, professional and energy-efficient designs that bring comfort and value to HVAC systems for Canadian residential and small commercial buildings.
For more information on HVAC DC, please click here.