Orion: Real-Life Performance of a Step 4, All-Electric Building
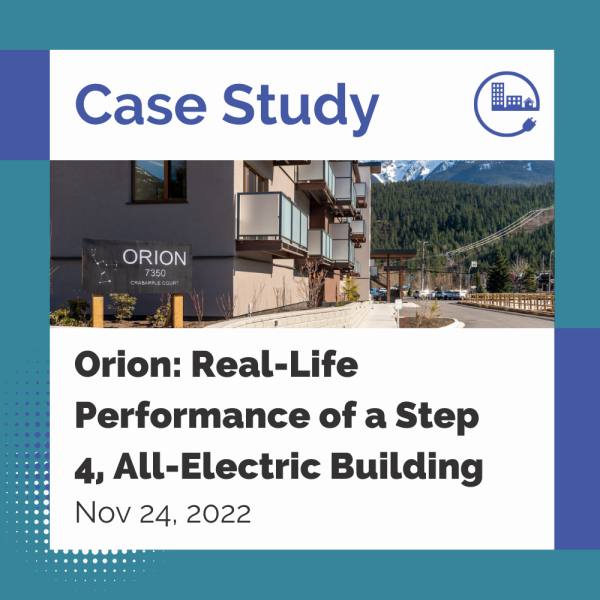
Innovation Building Group (IBG) is a developer/builder located in Whistler, BC. Using The 9 Foundations of a Healthy Building framework by Harvard University, IBG sets the design and construction goals for their projects. They have streamlined solutions to achieve these healthy building goals and integrated them with other project goals, such as energy and emissions performance.
They have successfully streamlined their construction process for high-performance buildings, resulting in lower construction costs. The most cost-effective projects are those where they act as the developer and builder because they have the most control over the process with this dual role. IBG has a prescribed set of construction methods and willingness to train trades on-site. They typically work with the same team of sub-contractors that understand their process and work to ensure that plans are easy to understand, and goals are communicated with every member in the project team to ensure quality and consistency. IBG’s formula also results in lower operating costs and superior comfort for the building occupant.
This article demonstrates the real-life performance of their 2020 Orion development in Pemberton, BC (located in Climate Zone 6 as defined by the BC Building Code).
Why all-electric?
At IBG, they no longer see a need for buildings to be connected to gas. Full electrification eliminates the need for typical gas infrastructure and associated trades, resulting in a reduction in both risk and cost.
In addition, newer, more airtight buildings are not a great place for gas-fired appliances, in particular gas cooktops. This is because the building code requires a range hood that vents directly to the outside. The range hood vent often compromises the air barrier system's continuity and worsens the building envelope's thermal performance. In addition, when the range hood is operating, it exhausts a significant amount of conditioned indoor air which must be replaced. This conditioning of the make-up air often increases the energy consumption of the building.
The latest research shows that indoor gas appliances can leak and produce more indoor pollutants than previously expected. Going all-electric is better for occupant health!
Staying ahead of the curve, building to the highest standards, and going all-electric ensures that buildings are resilient in a warming climate. This approach also ensures that the building owner is shielded from the financial consequences of emissions limits for existing buildings, which are starting to gain some traction in BC.
About Orion
Orion is a 45-unit, 3-storey for-sale condo building with underground parking. IBG was able to build this high-performance building better, faster, cheaper, and easier than typical construction. The design target was 50% less energy consumed for heating/cooling than a current Passive House or Step 4 of the BC Building Code. Additional design details can be found in this ZEBx case study.
In partnership with the British Columbia Institute of Technology (BCIT), every aspect of the Radius building envelope (IBG’s previous development in Pemberton) was modelled to identify the most cost-effective solutions for energy efficiency. Lessons learned from the Radius building were applied to Orion and IBG aims to continue to use or improve this model in each subsequent build. The solutions identified are simple:
- use the most efficient HRV/ERV,
- use the best-performing windows,
- use heat pumps to heat and cool the ventilation supply air,
- use a heat pump hot water system, and
- build an airtight high-performance building envelope.
This design offers resilience to extreme events, such as heat waves and wildfire smoke, by providing occupants with cooling, air filtration, and 100% fresh air for heating and cooling.
In addition, Orion encourages more climate-friendly transportation options by providing a 120V outlet in every parking stall and carport, which can be used for Level 1 electric vehicle (EV) and e-bike. Four Level 2 EV charging stations provide residents with faster charging options.
Keys to Going All-Electric
High-performance envelope
The high-performance and airtight building envelope reduces temperature fluctuations between different parts of the building which eliminates the need for sophisticated controls. The triple-glazed windows have a low solar heat gain coefficient and are operable. These features provide occupants with additional comfort control and reduce heating and cooling requirements. IBG evaluated the financial payback of multiple elements in the building and chose building methods and materials based on maximizing performance. While insulation is a key to high-performance buildings, it has a lower financial payback compared to airtightness, ERV performance, and eliminating thermal bridging which are low/no-cost measures.
An integrated, high-performance HVAC system
Orion’s centralized and integrated heating, ventilation, and air conditioning (HVAC) system includes a Swegon energy recovery ventilator (ERV) unit with 86% efficiency connected to two Mitsubishi variable refrigerant flow (VRF) air source heat pumps: 35 kW (10-ton) and 28 kW (8-ton). Choosing the most efficient ERV had the highest financial return for the project. The heat pumps allow the ERV to double its ventilation capacity and provide additional heating and cooling to respond to the peak demands. The ERV has a bypass mode to flush the heat out and help cool the building in summer when the exterior temperature is lower than the inside temperature, typically at night time. The high-performance building envelope and windows limit the daytime heating, allowing the night-time flush mode to perform much of the cooling. The cooling system relies on the thermal performance of the building envelope to keep the cooling load within the cooling capacity of the system.
While the HVAC system is centralized, supplemental backup heating is provided in each unit through 500W baseboard heaters with individual digital thermostat controls. A real-time data monitoring system provides input to the HVAC control system. This allows the building manager to optimize the performance of the central heat pumps and ERV, which minimizes the use of the less-efficient baseboard electric heaters. This has proven to be the most optimal choice in terms of cost and performance and is simple for the condo owners or building managers to maintain. Given that the design heat loss is 10.76 W/m2 (1 W/ft2), these small baseboards are capable of primary heating even though they are designed as the backup.
Heat pump water heating
Domestic hot water (DHW) heating is provided by SANCO2™ air-to-water heat pumps, which are part of a system that includes a series of storage and swing tanks. CO2 is a natural refrigerant with a low global warming potential (GWP). It is becoming increasingly popular as a refrigerant for climate-friendly water heating in BC. Hot water is produced at 66oC (150oF) and delivered at 49oC (120 oF) through a mixing valve.
Exterior SANCO2 units are whisper-quiet when operating
Is high-performance really better?
In a nutshell, absolutely. IBG is continuously measuring real-time performance on multiple systems – the primary and secondary heat pumps, ERV, heat pump water heater and electric resistance heater for the domestic hot water swing tank. Over the past two years, the Orion building has greatly outperformed the energy performance metrics for the highest level of the Energy Step Code for this building size.
Average performance for the previous two years:
This energy performance translates to a greenhouse gas intensity (GHGI) of approximately 1 kg CO2/m2 per year which is low enough to meet the highest level of the Province’s upcoming Carbon Pollution Standard for new buildings. If this building was in the City of Vancouver, it would meet the future carbon emissions limit of 3 kg CO2/m2 per year (effective July 1, 2023).
Operational costs are quite affordable. On a per unit basis, heating costs between $30 to $50 per year, cooling costs $15 to $30 per year (even in the 2021 heat wave where temperatures climbed to 46℃ in Pemberton), and water heating costs between $117 and $124 per year.
Image: System-specific energy use for 2021 and 2022
In addition to its low operating costs, according to this ZEBx construction cost study, Orion was built for approximately 30% less than the average code-minimum building in the region. As a best practice, IBG attempts to replicate its winning design and construction strategies with every development. Overall, they have 6 duplicable building archetypes in their repertoire, and the Orion design has been replicated three times.
Lessons Being Applied to Future Builds
Orion was the first IBG building to use Sanden heat pumps for domestic hot water. A lot of time was spent in the design phase to make the design strategy replicable for future developments. The short exterior water lines are heat-traced and extended into the units around the pump because on cold nights, if the water lines sit idle for too long, the pump can freeze. For this reason, all the Sandens run when there is a call for hot water to avoid idle time. One of the condenser units is installed in the mechanical room which enables it to work more efficiently with the warmer indoor temperature while cool the room at the same time. The back-up swing tank is heated by a Stiebel Eltron 36 KW boiler with a small circulating pump which was half the price of the original specification, a 120-gallon hot water tank with a 6KW element.
The electrical service is sized to meet the British Columbia Electrical Code (BCEC) standard with a 1,200 Amp, three-phase service There are zero load management issues, even with the EV charging. In four years of operation at IBG’s Radius building, the maximum load was 328 Amps. This begs a question, should the BCEC adjust the incoming service capacity requirements to account for the fact that new (and consequently, more energy-efficient) buildings will not require anywhere near as much amperage capacity as what has been historically required?
For this project, the Swegon ERV was sized generously for operating conditions falling in the mid-range for the unit. IBG is now reducing the ERV sizing to the maximum-rated capacity in boost mode. Boost mode only operates periodically in the summer for additional cooling.
—
Measuring operational performance is an essential part of both government and industry initiatives to decarbonize the building sector. It provides important feedback on whether the incentives, plans and regulations that the Province and local governments are employing to reduce emissions and increase energy efficiency are achieving the desired outcome. It also provides important feedback for developers, architects, consultants and builders on their decisions. For IBG, it confirms that many of their decisions have, in fact, resulted in real-life achievements. The operational data proves that Orion is a Step 4 building, provides comfortable living conditions in heat waves and cold snaps, and has much lower operational costs than a conventional code-minimum building. Orion provides excellent indoor air quality because of the ERV and the absence of gas-fired equipment within the units. The operational data also confirms that the cost-effective design strategies chosen for Orion can and should be used again. This project demonstrates that all-electric multi-family buildings are both feasible and cost-effective in cold climates.
__
IBG has developed a collection of modular, ready-to-build designs that cater to modern construction needs. While the designs are optimized for efficiency and streamlined workflow, they provide flexibility in key areas to suit specific project requirements.
The library can help save time, reduce costs, and maintain the highest standards of quality and sustainability.