Ravens Crossing: How a Community Went All-Electric
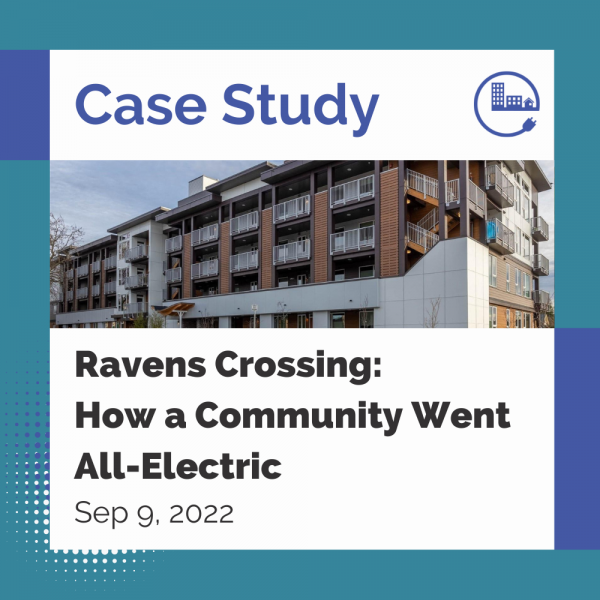
Ravens Crossing Cohousing is a recently completed, four-story residential development located in Sidney, BC. The complex contains 35 single-level units - all accessed from exterior walkways, a common space, and rooftop deck and garden. Built with sustainability in mind, Ravens Crossing achieved BUILT GREEN® Gold certification and was designed to be “healthy and operationally cost-effective, as well as energy, water, and resource-efficient”.
How it started…
The project launched in 2016 with a small group of like-minded individuals looking to create a community that supports connection. After visiting several cohousing communities, holding workshops, and hosting meetings, the Ravens (as they are now called) sharpened their vision “to build a sustainable community of introverts and extroverts in all ages and stages of life who value privacy and connection within a simpler, healthier, and more energy-efficient environment.”
Image 1: Ravens Crossing Cohousing, Sidney, BC
After securing a site in 2018, they began focusing on how they would achieve environmental sustainability, one of their core values. They settled on an initial design intent to aim for the BUILT GREEN® Gold standard. Cohousing projects work on cooperative consensus, which means that members strive to reach the best possible decision for the group. Hundreds of decisions were discussed and agreed upon by consensus including bylaws, community norms, and design details. Throughout the project development, some of the green building features could not be rationalized and were dropped to ensure that the construction costs stayed on-budget. Despite the removal of some of these features, the building still achieved its Gold status, as confirmed by energy modelling.
Image 2: Community planning workshops (Credit - Ravens Crossing website)
Why All-Electric?
The decision to exclude gas-fired appliances from the building was two-fold. First, natural gas extraction, distribution, and combustion results in the release of harmful greenhouse gases. This conflicts with the Ravens’ sustainability mindset. Second, avoiding the installation of gas lines within the building mitigated the risk of a fire or explosion following an earthquake. In addition, the Ravens chose to outlaw propane use on balconies to reduce the risk of a fire.
Green Building Features
Ravens Crossing is a 3,558 m2 (38,284 sq.ft.) residential development with 35 units, including 300 m2 (3,200 sq.ft.) of common space, a shared rooftop deck and garden, and a parking garage. To reduce energy consumption, some reliable design strategies were employed. These included positioning the building to take advantage of southern exposure, designing the south elevation with a high window-to-wall ratio to maximize solar heat gain, and specifying high-performance, triple-paned windows. The windows are from Starline’s 7100 series and the insulating glass units are filled with argon and include two low-emissivity coatings. The average fenestration U-factor is 1.05 W/m2·K (0.18 Btu/h·ft2·F). The walls are constructed using 38 mm x 140 mm (2” x 6”) wood framing with batt insulation in the cavities, resulting in an effective RSI value of 2.82 m2·K/W (R-16).
Image 3: The building has been designed to take advantage of Sidney's sunshine with south-facing terraces and generous windows. (Credit: Ravens Crossing website)
Each unit has its own Mitsubishi M-series horizontal-ducted heat pump for heating and cooling. The decision to use high-efficiency heat pumps (cooling SEER of 18, and heating HSPF of 12.6 (Region IV)) was based on reducing operating costs (compared to using electric baseboard heaters), quiet operation and providing cooling in the summer. Six small electric baseboard heaters were installed for supplementary heating in some areas of the basement and some rooms within the common area. Domestic hot water is generated by four A.O. Smith 450 L (120 US gallon) industrial electric water heaters.
Image 4: Heat pump condensing units on rooftop
With an all-electric design, the Ravens were initially concerned about the impact of power outages. After conducting research on the outage history, they determined that power reliability in the region was high. Given the unlikely scenario of a power outage, the Ravens decided to forgo the installation of a back-up power generator. If a power outage were to occur, the building envelope is likely to maintain a relatively stable indoor temperature for an extended period of time.
Solar photovoltaic panels were initially considered to reduce operational costs and improve resilience to power outages, but to keep construction costs from escalating, they were not included in the project. Provisions in the electrical system and structural supports in the roof were added to facilitate the addition of solar panels in the future.
Performance
Sidney, BC does not have a B.C. Energy Step Code requirement in place for new buildings. Nonetheless, the Ravens decided to pursue the BUILT GREEN® Gold Standard for energy efficiency. To ensure that the design would meet the standard’s performance target, an energy model was prepared by AME Group based on construction drawings. It was later updated to reflect as-built conditions. The updated energy model showed that the building is likely to be approximately 23% more energy-efficient than if it was built to meet the minimum requirements of Canada’s 2011 National Energy Code for Buildings (NECB). This level of energy efficiency allowed it to exceed the requirements for BUILT GREEN® Gold.
The modelled total energy use intensity (TEUI) for the building is 108.5 kWh/m2 per year. Relative to the Energy Step Code, this TEUI meets Step 3 for large residential buildings in this climate zone. The thermal energy demand intensity (TEDI) for the building is 52.6 kWh/m2 per year. Comparing it to the Energy Step Code, this is less than Step 2.
The modelled greenhouse gas intensity (GHGI) is 1.2 kg CO2/m2 per year. What makes this GHGI especially impressive is that it was achieved by a building with moderate energy-efficiency measures. This result is a testament to the fact that the most effective path to deep and immediate operational emissions reductions is quite simple - build an all-electric building. As an aside, the GHGI for this building is low enough to meet the highest level of the Province’s upcoming Carbon Pollution Standard for new buildings. If this building was located in the City of Vancouver, it would meet its future carbon emissions limit of 3 kg CO2/m2 per year (effective July 1, 2023).
Bill Way, one of Raven’s Crossings owners states:
“We couldn’t be happier with our cohousing community and our building. It has been lovely seeing the changing of seasons outside, while our indoor comfort has remained constant”
Lessons Learned
The original energy model included heat recovery ventilators (HRVs) to ventilate the units. Instead, the owners decided to invest in high-performance windows which allowed them to achieve the BUILT GREEN® Gold. The project architect, Peter Treheuit from Mobius Architecture Inc, stated “The use of triple-glazed, high-performance windows is an excellent envelope strategy to help with both energy performance and overall resident satisfaction with the internal climate of the units. Sound transmission is also lessened making a very quiet space.”
The desire to have each occupant pay for their own heating and cooling was a key consideration in choosing an individual heat pump for every unit. This is likely to reduce overall energy consumption because there is a direct correlation between the occupant’s heating and cooling habits and their utility bills. Overall, this increased the construction cost, in part because it was challenging to install all of the service lines in the walls and ceilings. For this reason, the architect is likely to recommend a centralized heating and cooling system for future clients. The operational costs could be included in monthly strata or maintenance fees.
Despite construction occurring through a pandemic, the building costs did not exceed the original budget and the project was completed ahead of schedule. The overall project cost was comparable to a new, code-minimum building in Sidney. Overall, the project team found cost-effective ways to achieve an all-electric building and the owners are thrilled with the outcome.