Reducing Carbon Through Heat Recovery
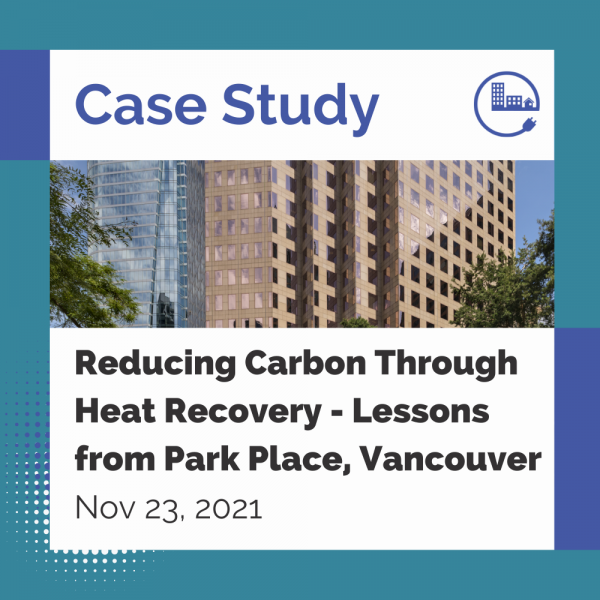
Lessons Learned from Park Place, an Iconic Vancouver Office Tower
Building electrification is identified as an important solution to mitigate the risks of climate change by removing or reducing the use of fossil fuels in buildings.
In British Columbia (BC), building electrification is embedded in the CleanBC plan and a key pillar of BC Hydro’s Electrification Plan. Despite the recent uptick in requests for energy studies focused on building electrification, the concept of building electrification is still relatively new in BC. The number of projects moving to implementation is slowly rising, however, and there is increased importance in sharing best practices on building electrification. The following example focuses on addressing real-life challenges, the importance of involving the building operator throughout the project and establishing best practices.
Project Background
Park Place is a mixed-use office building in downtown Vancouver managed by QuadReal Property Group. The 65,300 m2 (703,000 ft2) building houses QuadReal’s global headquarters, 2,200 office occupants and a retail mall containing shops, services and a restaurant. QuadReal has adopted a science-based climate target for their Canadian portfolio: an 80% reduction in carbon emissions by 2050 compared with their 2007 baseline. QuadReal aims to be a global sustainability leader and on their pathway to reduce emissions, their intention is to mitigate future risks related to climate change. Investing in their existing building stock helps them to remain competitive with new commercial properties and provide high quality, comfortable and productive environments for tenants.
Prior to the implementation of the heat-recovery chiller (HRC) project described below, QuadReal’s continuous optimization program at Park Place led to a number of retrofits which achieved energy savings of 25% and reduced greenhouse gas (GHG) emissions by 19% below the 2007 baseline.
Image 1: Park Place exterior views, Vancouver BC
The Opportunity
Mixed-use office buildings are a great application for HRCs due to the simultaneous demand for heating and cooling throughout the year. Park Place is heated via a natural gas-fired district steam system. The opportunity to reclaim heat from the chiller systems was identified by the building operator and representatives of the chiller manufacturer, Trane, during a routine service appointment. QuadReal enlisted the help of engineering consultant, SES Consulting, to complete further analysis and design for the system. This project resulted in adding two HRCs, one Trane, model RTWD, water-cooled helical rotary chiller, and a Multistack, model MS050A, high temperature water-cooled modular chiller. The HRCs reclaim heat that previously was released to the atmosphere through cooling towers and reduce the amount of district steam required in the space heating system.
Managing the Electrical Load
One of the challenges that building owners face when electrifying building systems is the additional electricity consumption and associated operating costs. At Park Place, QuadReal was able to avoid these costs by addressing other electrical inefficiencies within the building to offset the added load. The HRC project would have resulted in a 3.1% increase in electricity use (330,000 kWh); however, an LED lighting retrofit in the building was able to offset the load by 4.5% (475,000kWh) resulting in an overall 1% decrease in electricity consumption. As a result of the reduced overall electricity and steam consumption, the operational costs decreased.
Involving the Building Operator
Park Place’s Operations Supervisor was instrumental in the development of this project by introducing the opportunity to QuadReal and by participating in the planning, investigation, and commissioning of the project. Building operator buy-in at the outset of a project is essential to the success of any project. In the case of Park Place’s new HRC system, the Operations Supervisor was involved in commissioning the project and trained by Trane, leading to a fully-automated, smooth-running system. New systems and equipment can be more complex that those they are replacing. Building operator buy-in and commitment ensures that minor challenges are addressed in an efficient manner. Operator training on the new equipment is an important success factor to ensure that the new system operates smoothly and reliably on a daily basis.
Image 2: Park Place Interior, Vancouver BC
Lessons Learned
With every project, there is an opportunity to reflect: What could we have done differently?
While the Park Place HRC project is deemed a success, there are a number of lessons that can be shared with others embarking on similar projects. While steam savings were achieved, they were substantially less than initially modeled due to a design challenge with the existing piping. The original model intended to reclaim heat from both the chiller condenser loop and the tenant condenser loop; however, the tenant loop did not respond according to the modelled assumptions making it ineffective for heat recovery. As the engineering model of the HRC assumed that heat could be recovered from the tenant loop 24/7, the original estimate of 80% steam savings was not realized. More technical details on the initial design can be found in an earlier case study by the City of Vancouver.
The following section highlights the lessons learned from this project:
- The Maximum Heating Supply Water Temperature provided by the HRC equipment limits how often the equipment can operate. In older buildings hot water temperature reset poses challenges. In the case of Park Place, which was built in 1984, attempting to lower the building supply water temperature resulted in a much longer warm-up time for the building. As a result, the full savings related to the use of reduced supply temperature were not realized.
- Collect as much pre-retrofit data as possible. During the modelling investigation, it was assumed that heat could be recovered from the 24/7 tenant loop, which in practice turned out not to be feasible. Additionally, the model was based on Park Place having an after-hours heating demand; while after-hours heating was in place at one point, this practice was eliminated via ongoing optimization efforts. As such, the modelled night-time waste heat from the tenant loop and opportunity for reduction in night-time heating was no longer available and initial savings were overestimated.
- For tall buildings (greater than 20 stories high) water pressure may exceed equipment ratings. The manufacturer’s recommended equipment was not compatible with the head pressures occurring in the system and several modifications were required to account for this after the purchase. Longer modelling timeframes and additional investigation could have identified this issue prior to implementation.
Through this project, a new best practice for modelling was developed by SES Consulting: A minimum of one-year of building automation system (BAS) data should be analyzed pre-retrofit including the use of a granular time-of-use submeter. The model must include the full picture of mechanical systems and all possible feedback loops
Image 3: Park Place Interior, Vancouver BC
The Savings
The Park Place HRC project was implemented in 2018 and has led to a 23% reduction in GHG emissions to the tune of 227 tCO2e/year and annual energy consumption savings of 8% (883,000 ekWh/year). Annual utility cost savings from electricity, steam and water consumption are $60,000. The original project payback period was estimated at 10 years and is now expected to be slightly longer, however, anticipated carbon tax escalation will improve that timeline.
Park Place now has a GHG intensity (GHGi) of 10.65 kg CO2e/m2 down from 15.92 kg CO2e/m2 in 2018. With the energy conservation and GHG reduction measures undertaken since 2007, the building has achieved a GHG reduction on the order of 50% below the 2007 baseline.
A B2E collaboration with QuadReal Property Group