Is Using a Heat Pump in the North Feasible?
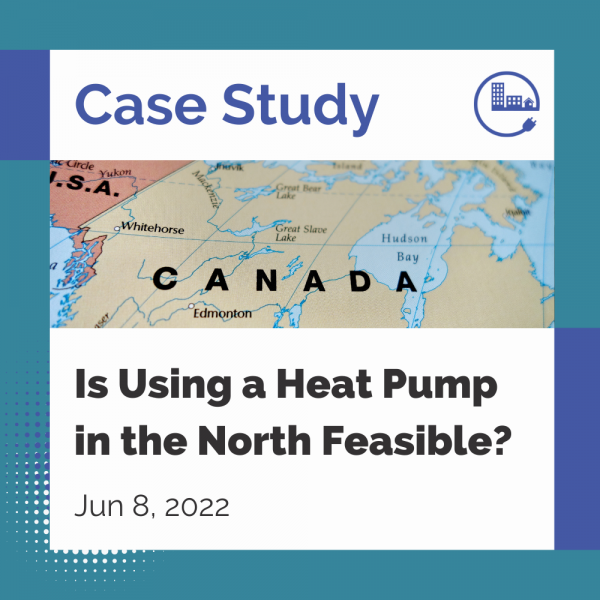
Is Using a Heat Pump in the North Feasible?
Climate Zone 7A in British Columbia is the province’s cold north. It includes communities such as Burns Lake, Dawson Creek, Smithers, and Fort. St James. With winter design temperatures in Fort St. James at a frigid -32.7 °C (-27°F), it would be understandable to assume that heating a new home in this location with a heat pump would be a challenge at the very least. Yet, Northern Homecraft has done this consistently with many of their custom-built homes in Fort St. James and surrounding area. In essence, all it takes is good planning, coordination, and motivation.
Good design practices are a prerequisite for any system. A zero-emissions goal is one motivation, and another motivation could be compliance. In all cases, choosing the right heat pump is part of good design practices.
Image 1: Map of Fort St. James with key in CZ 7A.
The Hodder Residence is a 315 m² (3383 ft²) single detached home in Fort St. James. From an energy modelling perspective, the home has a complex geometry and a high window-to-wall ratio. It isn’t a simple, small box.
Image 2: The Hodder Residence blueprints. Full details available here.
Despite its size, geometry, glazing, and location, this house was built to the BC Energy Step Code’s highest level 5, and therefore Net Zero ready. From the perspective of a mechanical designer, this level of energy performance for the home is the most significant design criteria that allows a simple heat pump as the primary heating source. This is not to suggest that a home in Canada’s colder climate zones must be built to the highest energy efficiency to make a heat pump viable. It just makes it easier.
Homes with larger heating loads create more challenges such as the range of product capacities available on the market, auxiliary heat requirements, and sizing of duct systems.
Integrated Design Process (IDP)
The energy performance target of this home was determined through an Integrated Design Process (IDP), where the critical decisions and design strategies are coordinated early in the project while all options are still available. The team in this case included the homeowner, builder, house designer, energy advisor, mechanical designer, mechanical installer, solar designer and electrician.
The team met online before construction to discuss and consult on the key parameters that will influence the successful outcome of the project, including the optimization of:
- Energy Performance
- Budget
- Occupant Comfort
- Aesthetics
- Resilience
Armed with the energy model (HOT 2000) results including several iterations, and proper load calculations (CSA F280-12), Ecolighten was equipped to provide the team with accurate analysis and cost/benefit scenarios for consideration.
Image 3: Calculations for the Hodder Residence energy rating.
A cost analysis for the mechanical options included:
- Conventional gas furnace with A/C (air conditioning) & ERV (energy recovery ventilator)
- Cold climate heat pump, electric back-up & ERV
- Ground source heat pump (geothermal), with horizontal loop field & ERV
Option 1 had the lowest installation cost, while Option 3 had the highest. Maintenance costs of all options were very similar. Weighing the capital cost against the operating cost over the lifecycle of the equipment, option 2 had the best payback.
Cold Climate Heat Pumps
A typical cold climate heat pump’s rated capacity is relatively consistent to -15°C (5°F). In practice we have seen it maintain capacity as low as -20 °C (-4°F). In addition to maintaining its capacity at sub-zero temperatures, these heat pumps also maintain a high efficiency at these low temperatures. Since the introduction of cold climate heat pumps into the market, they are becoming the favoured option in any climate beyond Climate Zone 4. Although there is a small premium cost for a cold climate heat pump, it is not significant compared to its value.
Image 4 (top): Information tables and performance specs of Mitsubishi Electric heat pump. Image 5 (bottom left): Mitsubishi Electric heat pump installed outside residential building. Image 6 (bottom right): Mitsubishi Electric heat pump in cold climate.
Both the capacity and efficiency at sub-zero temperatures reduces the amount of back-up or auxiliary heat required, such as electric strips or baseboards.
There were other factors to consider beyond mechanical system costs that ultimately led to the decision to build a Step 5 home with a cold climate heat pump as the primary energy source for heating and cooling:
- Building the house to Step 5 had cost implications, although a portion was offset by reduced mechanical system costs and generous rebates.
- The owner’s motivation to lower their carbon footprint was a strong influencing factor.
- Building a house to meet the province’s established, future minimum energy efficiency requirements would likely increase the resale value relative to a home built to meet the current minimum BC Building Code requirements.
- Better retained investment value in the future market given that the house was adapted to the evolving regulatory standards of electrification.
- Obtaining a known label and branding for the energy performance of the home (CHBA NetZero Ready and Step 5 compliant) was an attractive proposition.
- Finally, the tangible benefit of optimized comfort with a low operating cost.
Equipment Selection
After consensus was reached for an overall design strategy, the next challenge was to select the equipment. Beyond brand quality and competitive pricing, in smaller and remote communities, careful consideration must be given to:
- Supply chain.
- Are the equipment and its replacement parts available locally?
- Is there local technical support?
- Trade knowledge and experience.
- Are there contractors available who are familiar and experienced with the proposed equipment?
- Will it be necessary to hire contractors from other communities and incur extra travel costs and scheduling disruptions?
- Will there be a quick response time in case of system breakdowns?
- Electrical Service Capacity.
- All electric homes, in combination with electric vehicles, lead to greater power demand and a potential need for larger electrical panels.
- Amount of electrical load required by heat pump to run the compressor and fans vs. the load required for electrical back-up systems.
- Cold climate heat pumps provide the extra benefit of not requiring as much auxiliary heat, and therefore help reduce the strain on the electrical panel.
Ultimately the mechanical equipment package consisted of a:
- Mitsubishi P-Series H2i cold climate heat pump with a rated 48,000 Btu/hr (14Kw) capacity at -15°C (5°F), which consists of a PUZ-HA42NKA outdoor unit combined with a PVA-A42AA7 indoor unit.
- Venmar ERV E15 140 cfm and 67% sensible recovery efficiency.
The ventilation system was integrated into the forced-air system thereby combining the Mitsubishi with the Venmar ERV.
System Design
As part of the IDP, an articulated mechanical system design was created and coordinated to deliver the comfort and performance expectation, in a manner that weaves through the building and its structure with the least amount of impact on the architectural aesthetic of the home.
A design is 'articulated' when it is drawn over and integrated with architectural/structural plans with all details. This is not yet common practice.
Image 7: Hodder Residence home performance design. Full details available here.
The HVAC system was divided into four 4 independent zones, each with a thermostat controlling a damper in the ducting.
To minimize envelope penetrations, the ERV system was adapted to a Posh™ system (boost function), to allow the ERV to act effectively as bathroom exhaust, removing the need for dedicated bathroom fans.
Quality Assurance
Throughout construction, the mechanical installation was reviewed for quality of work and consistency with the design intent. During construction, several changes to the design were coordinated and implemented by design and the construction teams. When construction was completed, a final review was done of all components. They were also commissioned to ensure that their actual performance matched the design targets. All warranty, service, maintenance, as-builts, manuals, and start-up procedures and tests documentation were reviewed.
The handover to the homeowners concluded a process which has ensured efficiency and comfort since January 2021. See this BC Hydro article on the homeowner perspective in their all-electric home.
Conclusion
Is using a heat pump in the north feasible? Is it as cost effective as a code-minimum home when you include operating costs? Is it as reliable and comfortable?
Northern Homecraft has successfully applied this same process many times on a variety of homes in this northern region, each with different sizes, budgets, and expectations. This project, and many others, clearly demonstrate that a heat pump is not only feasible, but also cost effective, reliable, and comfortable for the majority of homes. In fact, using heat pumps in cold climates is a good idea.
Northern Homecraft’s co-owner, Shay Bulmer, offered additional insight that is applicable to large homes in cold climates:
“While I agree with the conclusion that these homes are technically feasible and we are able to build them for a variety of budgets, it is also true that all-electric homes of this size and complexity may find that the maximum available electrical service may be taxed or maxed, even at 200 AMPs. This can result in costly upgrades to the existing infrastructure, or a second costly 100 or 200 AMP service to be run into the property, to accommodate for additional loads such as an EV charger (not yet present in this home) or a hot tub. One solution we are considering is smart load management that would see certain loads circumstantially shed or inhibited, while others are prioritized so that loads can never exceed the maximum at any given moment. These features will come at a cost but may allow us to solve our issue of having to incorporate and cover the load of a supplemental heat source in our colder climate. As these features would not be required to build a home to a code minimum standard with a gas heating source (removing the substantial electrical heating load), the premium to incorporate them still needs to be acknowledged.”
A B2E Collaboration with Ecolighten
Primary Author: Rob Pope
.